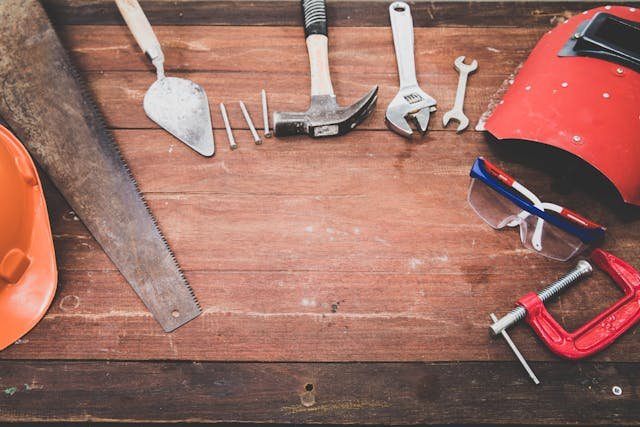
Equipment is essential for productivity in various settings, including construction, workshops, and home projects. Maintaining its seamless operation guarantees that your work remains effective, thus preventing unplanned downtime that may throw off budgets and cause financial and time losses. Preventive maintenance is about increasing the life of your tools and equipment, not only about repairs. Through regular maintenance, you preserve your investment and keep everything running at its best, therefore reducing wear and strain resulting from negligence.
Regular Inspections Prevent Long-Term Damage
Preventive maintenance mostly consists of regular inspections. Thoroughly looking for wear, leaks, or misalignment in your equipment helps you identify possible problems before they start expensive repairs. These inspections not only save money but also ensure safety, as worn or loose parts can cause accidents. Pay close attention to areas that experience regular movement or high degrees of friction since, over time, these are more likely to suffer damage. Reviewing the equipment also helps you to maintain track of its performance and address minor inefficiencies. Early intervention reduces strain on the machinery, keeping it in top condition. Regular inspections not only ensure the dependability of your equipment but also provide you with confidence that it is ready to undertake challenging tasks without fail.
Lubrication Reduces Wear and Tear
Reducing unnecessary wear on moving components depends critically on proper lubrication. Unchecked friction between components can cause overheating, lower efficiency, and, eventually, breakdowns. Using high-quality lubricants, such as multi purpose oil, ensures that all parts run smoothly and extends the life of your machinery. This type of oil works effectively in many different applications, therefore simplifying maintenance across several equipment. Applying the appropriate amount of lubricant at regular intervals forms a protective barrier, reducing direct contact between surfaces. This lowers wear as well as corrosion, which can endanger your equipment’s structural integrity, including appropriate lubrication in your regular maintenance guarantees the best performance and lifetime by keeping everything running smoothly.
Cleaning Enhances Performance and Longevity
On and inside your equipment, dirt, dust, and debris can build up to cause blockages, overheating, or decreased efficiency. Prevention of these contaminants from affecting the operation of your apparatus depends on regular cleaning. Pay close attention to places like vents, filters, and exposed parts since they generally gather most debris. Neglecting cleanliness can accelerate wear and make your equipment work harder than necessary, shortening its life. Cleaning also gives you a chance to closely examine your machinery since the practice increases your chances of identifying problems, including cracks, loose components, or unusual wear. Combining cleaning with routine inspections results in a complete maintenance schedule that guarantees your equipment stays reliable under heavy use and guards against preventable damage.
Scheduled Maintenance Keeps Equipment Reliable
Every piece of equipment comes with a recommended maintenance schedule meant to maximize its performance. Following this schedule ensures that all components are serviced before they show significant wear or failure. To guarantee everything operates as it should, scheduled maintenance sometimes includes tasks like adjusting settings, testing performance levels, or replacing worn-out parts. By scheduling your maintenance tasks ahead of time, you lower the chance of unplanned malfunctions that could cause expensive downtime and disturb processes. It also lets you plan for any maintenance, so maintaining the seamless running of your business. Following a consistent maintenance program shows proactive care for your equipment, therefore guaranteeing its dependability and efficiency for many years to come.
Training Ensures Proper Equipment Use
Even the best-maintained equipment can be damaged if used incorrectly. Making sure everyone running the machinery is adequately qualified helps to avoid misuse, which usually results in unneeded wear and tear. Training covers knowing the capabilities of the equipment, its limitations, and operating and maintenance manufacturer standards followed. Educated operators are also more likely to notice when something isn’t working properly, allowing for earlier detection of potential issues. This awareness lowers the possibility of extended use, which can aggravate injury. Prioritizing training not only helps to preserve your equipment but also increases overall safety and productivity during its use.
Conclusion
Preventative maintenance is a proactive approach to keeping your equipment in top condition, ensuring dependability, and extending its life. From routine inspections and appropriate lubrication to complete cleaning, planned maintenance, and operator training, every action helps to maximize performance and reduce the likelihood of unanticipated problems. Consistent maintenance protects your investment and ensures the efficiency you need to get the job done. With these strategies, you can keep your equipment running smoothly, regardless of the demands.