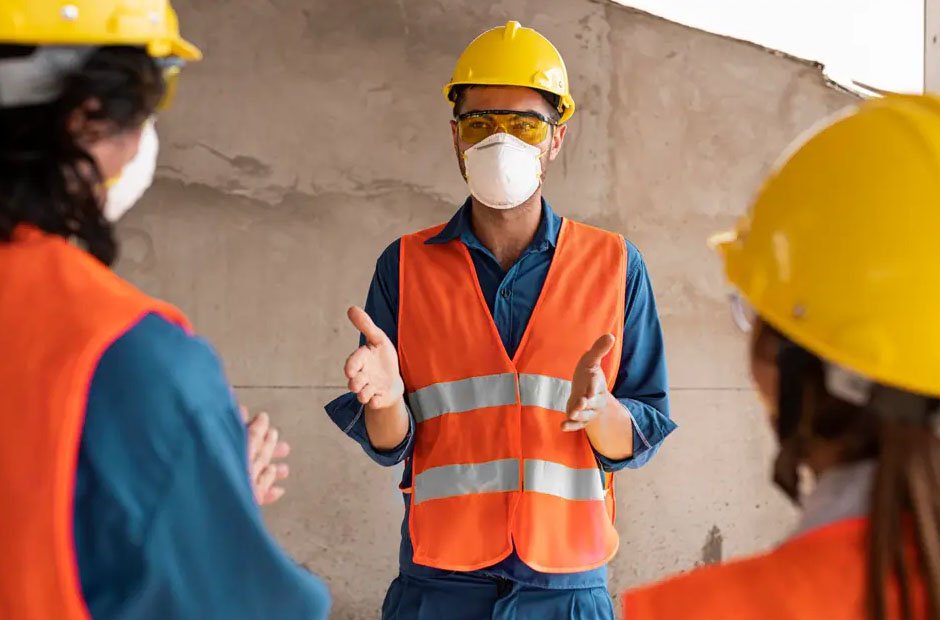
Safety at the workplace isn’t just about following regulations; it’s about protecting lives and preventing injuries. While every industry faces unique risks, working at heights introduces particular hazards that make quality equipment indispensable.
For businesses that rely on lifting or accessing elevated areas, using safe and reliable equipment is important. Let’s explore why prioritising top-notch access tools is crucial for safety.
Ensuring Stability and Reliability
Quality access equipment provides stability, ensuring workers can perform tasks confidently and safely. Substandard tools may falter under pressure, potentially leading to falls or injuries.
High-quality ones, however, are designed with rigorous safety standards, offering features like enhanced grip, reinforced platforms, and automatic shutoffs to prevent tipping or collapsing. Investing in reliable tools minimises risks and reinforces a safety-first approach.
Complying with Safety Regulations
Strict industry standards govern equipment safety, especially when it comes to working at heights. When businesses use quality tools, they’re more likely to comply with these regulations, reducing the likelihood of penalties and ensuring a safer workplace. Quality equipment is regularly updated and tested to meet or exceed these standards, meaning that businesses using these tools are better protected from legal risks.
Reducing Maintenance Hassles and Downtime
- Reduced Maintenance Needs: Quality equipment generally requires less frequent maintenance. Lower-grade tools may save costs initially but often lead to more breakdowns, leading to downtime and repair costs.
- Longer Lifespan: Reliable equipment built with high-grade materials lasts longer and performs better over time, contributing to workplace productivity and safety.
Promoting Efficiency and Comfort
Using high-quality access equipment not only protects workers but also enhances their productivity. When workers can rely on their equipment, they can focus more on the task at hand rather than worrying about potential hazards.
Ergonomic designs in modern tools also promote worker comfort, reducing fatigue and improving efficiency. This means employees can work safely and efficiently, leading to faster project completion and higher overall productivity.
Minimising Risks of Injuries and Fatalities
Working at heights is inherently dangerous, and accidents often result from equipment failure. Quality tools are designed to prevent such failures with features like anti-slip surfaces, secure harness points, and advanced control systems. These features significantly lower the risk of falls and other injuries, making high-grade tools an essential component of any safety plan.
Encouraging a Safety Culture
When a company invests in quality equipment, it sends a message that employee safety is a priority. This attitude promotes a culture of safety within the organisation. Employees are more likely to follow safety protocols and take precautions seriously when they see their employer valuing their well-being. A positive safety culture reduces accidents, enhances morale, and can lead to lower insurance costs due to fewer claims.
Reduced Liability and Legal Risks
In addition to creating a safer environment, quality tools help companies mitigate liability and avoid costly legal disputes. If an accident occurs due to equipment failure, the organisation could face lawsuits, compensation claims, and severe penalties.
Quality tools are less likely to fail, reducing the risk of workplace injuries and potential litigation. Investing in top-tier equipment demonstrates a company’s commitment to safety and its responsibility towards its workers, which can be a crucial factor in legal proceedings. Proactively reducing the risk of incidents helps companies avoid the financial and reputational damages associated with workplace accidents.
Features that Enhance Safety
- Automatic Shutoff: Prevents tools from operating if a safety hazard is detected.
- Stabilising Outriggers: Adds stability to prevent tools from tipping over, especially on uneven terrain.
- Harness Attachments: Allows workers to secure themselves properly, reducing fall risks.
- Anti-Slip Platforms: Ensures workers have secure footing even in wet or slippery conditions.
Quality access equipment is about more than just meeting regulatory standards. It’s a proactive step toward safeguarding employees and ensuring that each workday ends without incident. By prioritising safety and investing in reliable equipment, businesses create a safer work environment, foster a culture of care, and, ultimately, build a foundation for long-term success.
Author: Clarie Hank