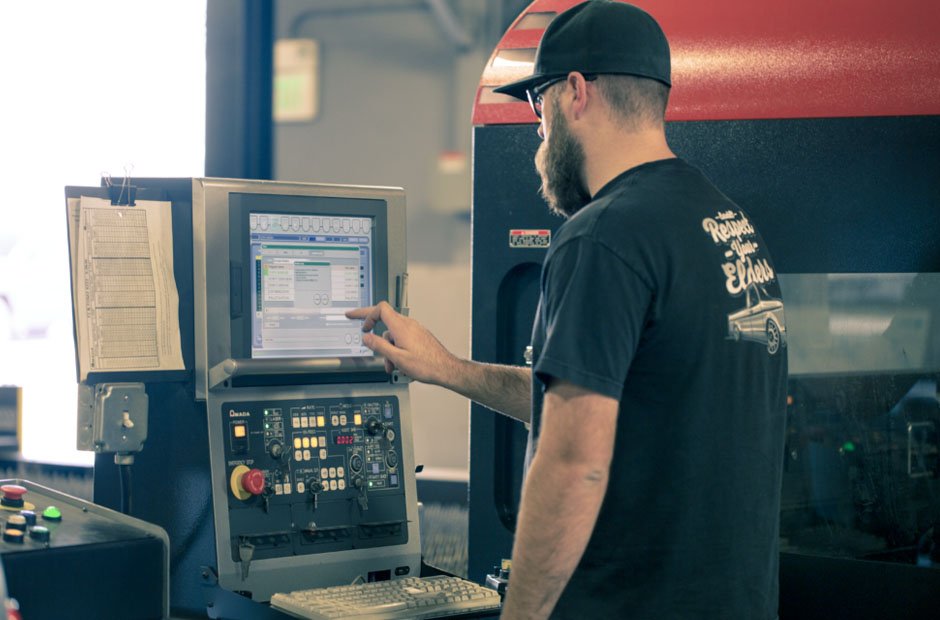
The manufacturing of computer components is a precision-driven process that demands meticulous attention to detail and high levels of accuracy. As the computer industry continues to evolve with rapidly changing technologies and increasing consumer demands, industrial automation has become a critical factor in enhancing production efficiency, reducing costs, and maintaining the high quality of products. Among the various technologies driving these advancements, servo drives and controllers are crucial for achieving precise control over the automated manufacturing processes. If you’re interested in knowing more about product prototyping services make sure you visit Paraform.
Importance of Automation in Computer Components Manufacturing
The manufacture of computer components such as processors, motherboards, hard drives, and memory units involves complex and intricate processes. Each component must meet strict specifications to ensure proper functionality and compatibility with other parts. Automation provides the necessary tools to meet these requirements consistently and efficiently.
- Precision and Consistency: Automated systems equipped with high-precision tools and robotics are capable of performing complex assembly tasks with greater accuracy than manual processes. This precision is essential for the miniaturization of components like microprocessors and memory chips, where even microscopic errors can render a device faulty.
- Scalability and Flexibility: Automation allows manufacturers to quickly adjust production lines to new specifications and changes in product design, which is critical in an industry characterized by rapid technological advancements. This flexibility helps manufacturers stay competitive by reducing time-to-market for new products.
- Cost Efficiency and Productivity: Automated systems significantly enhance productivity by enabling continuous operations and reducing the dependency on human labor. This not only lowers production costs but also minimizes human error, further improving the overall efficiency of the manufacturing process.
Role of Servo Drives and Controllers
Servo drives and controllers play a pivotal role in the automation of computer component manufacturing. These devices provide precise control over the movement and speed of the machinery involved in the assembly lines. Servo technology is particularly important in applications requiring intricate movements, such as the placement of tiny electronic components on circuit boards.
- High-Speed Assembly Lines: In the production of computer components, speed and accuracy are critical. Servo drives control the motors that power conveyor belts and assembly arms, ensuring that components move through the assembly line smoothly and are precisely aligned for assembly, soldering, or inspection.
- Precision Placement: The mounting of chips on motherboards and the assembly of hard drive components require extremely precise movements. Servo controllers, such as the dkc11.1-040-7-fw, regulate the position and speed of robotic arms to place components accurately, reducing the risk of misalignment, which could compromise the functionality of the final product.
- Quality Control: Advanced imaging and diagnostic equipment used in the quality control processes are often powered by servo systems. These systems adjust the position of cameras and sensors with high precision, allowing for detailed inspections of tiny components at various stages of the manufacturing process.
Challenges in Automating Computer Components Manufacturing
While the benefits of automation are clear, there are several challenges that manufacturers must address to fully leverage these technologies:
- High Initial Investment: Implementing state-of-the-art automated systems requires significant capital investment. The cost of acquiring and installing advanced robotics, servo-driven machinery, and control systems can be prohibitive, especially for smaller manufacturers.
- Technical Expertise: The complexity of automated systems necessitates a high level of technical expertise. Manufacturers must either train their existing workforce or recruit skilled professionals who can operate and maintain these sophisticated systems.
- Integration Complexity: Integrating new automated systems into existing manufacturing processes can be challenging. It requires careful planning to ensure compatibility with older equipment and systems, as well as minimal disruption to ongoing production.
- Cybersecurity Risks: As manufacturing processes become more interconnected and reliant on data, the risk of cybersecurity threats increases. Protecting sensitive manufacturing data and operational technology from cyber-attacks is a growing concern for the industry.
Future Trends in Automation for Computer Components Manufacturing
Looking forward, several trends are likely to influence the future of automation in computer components manufacturing:
- Machine Learning and AI: Artificial intelligence and machine learning are expected to play a larger role in automating decision-making processes. These technologies can enhance predictive maintenance, quality control, and even design optimization by analyzing vast amounts of production data.
- Internet of Things (IoT): The integration of IoT technology can further enhance operational efficiency by enabling real-time monitoring and control of manufacturing equipment. IoT devices can collect and analyze data from various points in the production process, providing insights that can be used to optimize operations.
- Sustainable Manufacturing: As environmental concerns become more pressing, there is a growing focus on making manufacturing processes more sustainable. This includes reducing waste, using energy-efficient technologies, and recycling materials.
Conclusion
Industrial automation, driven by technologies such as servo drives and controllers, is revolutionizing the manufacturing of computer components. By enhancing precision, efficiency, and flexibility, automation helps manufacturers meet the high standards of quality and innovation required in today’s competitive computer industry. As technology continues to evolve, the integration of advanced automation solutions will be crucial for manufacturers seeking to optimize their production processes and maintain a competitive edge in the global market.