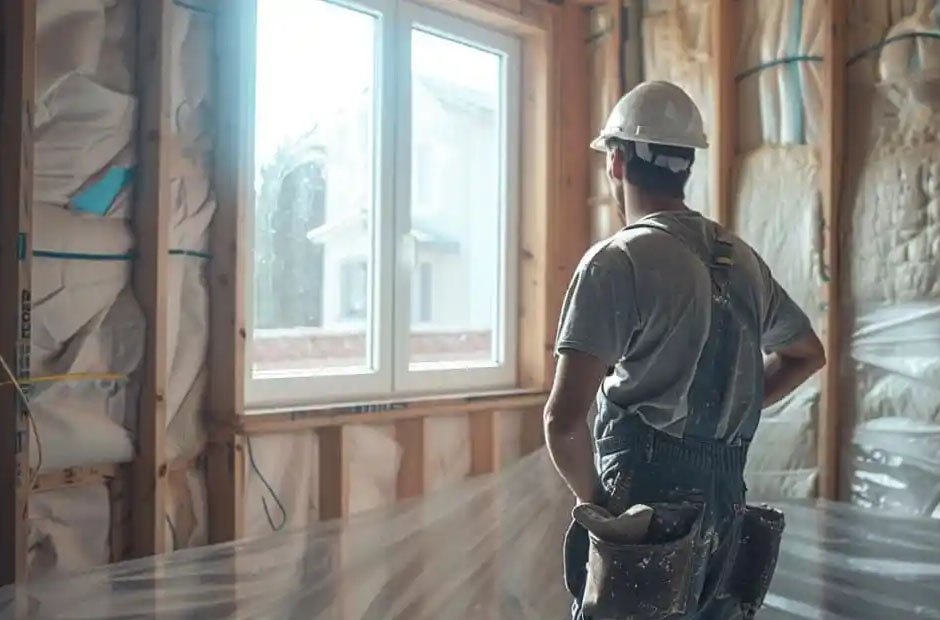
Ensuring safety during insulation installation is paramount for workers and homeowners. An insulation company recognizes that a well-planned installation process minimizes risks and maximizes efficiency. This involves a combination of proper training, adherence to safety regulations, and the use of appropriate materials and equipment. We will explore the various safety measures an austin insulation company implements to create a secure working environment and ensure the well-being of all involved.
Training and Certification of Installers
The foundation of safety in any insulation project begins with the training and certification of the installers. Insulation companies often require their employees to undergo rigorous training programs that cover safety protocols, proper handling of materials, and the use of specialized equipment. These training sessions typically include classroom instruction and hands-on practice to ensure workers understand the theoretical aspects and practical applications. Certification programs also often require knowledge of local and national building codes, which helps installers comply with regulations.
Moreover, continuous education is critical in this field. As new insulation materials and technologies emerge, companies ensure their installers stay updated through ongoing training. This commitment to education helps workers identify potential hazards and apply the safest techniques during installation. By investing in comprehensive training and certification, insulation companies create a workforce that understands safety practices and prioritizes them in every project.
Use of Personal Protective Equipment (PPE)
Personal protective equipment (PPE) is vital in maintaining safety during insulation installation. Insulation companies enforce strict policies regarding PPE, ensuring every worker is equipped with the necessary gear before entering a job site. Common PPE items include gloves, masks, goggles, and hard hats. Gloves protect the hands from sharp edges and irritating materials, while masks prevent inhaling dust or fibers that may harm the respiratory system.
Goggles are crucial for protecting the eyes from particles that may become airborne during installation. Hard hats safeguard against head injuries from falling objects, a concern in construction environments. Insulation companies also stress the importance of regularly inspecting PPE for wear and tear and replacing damaged items immediately. By implementing a robust PPE program, these companies create a layer of protection that significantly reduces the risk of injury during installation.
Compliance with Safety Regulations
Insulation companies must adhere to local, state, and federal safety regulations governing construction practices and worker safety. Compliance with these regulations is not merely a legal obligation; it is a fundamental aspect of ensuring the safety of both workers and homeowners. Companies typically conduct regular audits to verify compliance with safety standards, such as those set by the Occupational Safety and Health Administration (OSHA) in the United States.
These audits may involve reviewing safety practices, assessing the condition of the work environment, and ensuring that all necessary permits are obtained. Insulation companies also often designate a safety officer responsible for monitoring compliance and addressing potential safety concerns. By staying compliant with safety regulations, insulation companies protect their workers and ensure that homeowners are not exposed to hazards that could arise from improper installation.
Implementing Safe Work Practices
In addition to training and compliance, insulation companies establish safe work practices tailored to the specific needs of each project. This may involve assessing the work environment before installation begins, identifying potential hazards, and developing mitigation strategies. For instance, when working in confined spaces or attics, companies may implement additional safety measures such as using harnesses or providing adequate ventilation to prevent the accumulation of harmful gases.
Communication is also a key component of safe work practices. Insulation companies often hold pre-installation meetings where workers can discuss potential hazards, review safety protocols, and clarify their roles in ensuring safety. This fosters a culture of safety awareness, where workers feel empowered to speak up if they observe unsafe conditions. Insulation companies can effectively reduce accidents and injuries on job sites by creating a systematic approach to safe work practices.
Quality Control of Materials and Equipment
The materials and equipment used during insulation installation are crucial to safety and effectiveness. Insulation companies conduct rigorous quality control checks on their materials, ensuring they meet safety standards and performance criteria. This includes verifying that insulation products are free from hazardous substances, such as formaldehyde or asbestos, which can pose serious health risks to installers and homeowners.
Additionally, the equipment used for installation, such as blowers and cutting tools, must be maintained in optimal condition. Regular inspections and maintenance routines help identify any issues that could lead to accidents or malfunctions during installation. Companies often provide training on the proper use of equipment, emphasizing the importance of following manufacturer guidelines to prevent injuries. Insulation companies can ensure a safe and effective installation process by prioritizing quality control.
Safety measures during insulation installation are not just guidelines; they are essential practices that protect workers, homeowners, and the integrity of the installation itself. Through rigorous training, the use of personal protective equipment, compliance with safety regulations, implementation of safe work practices, quality control of materials and equipment, and thorough emergency response planning, insulation companies create a culture of safety that benefits everyone involved. Ultimately, a commitment to safety is an investment in the quality of work and the well-being of all parties.