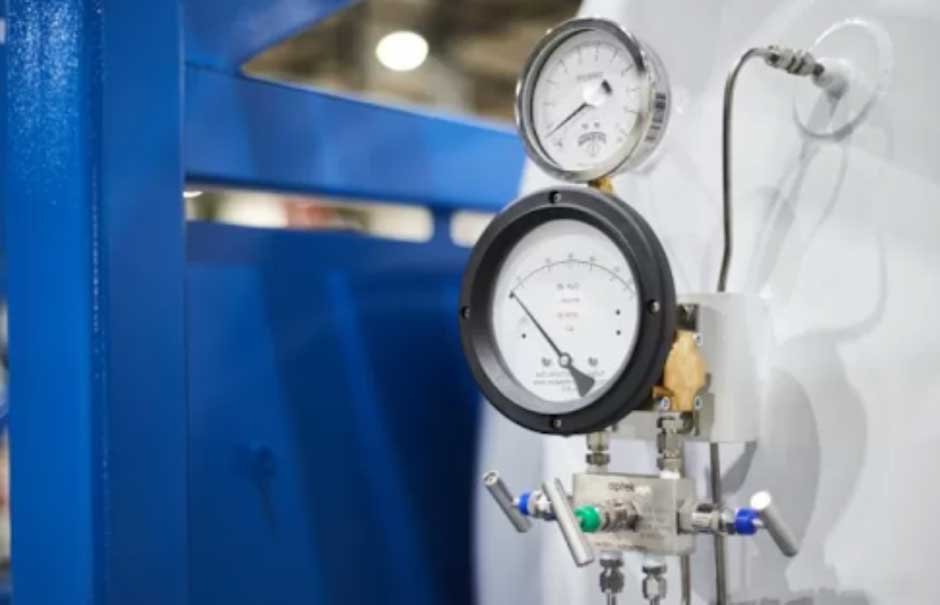
Optimize safety and operational efficiency with advanced pressure monitoring technologies. Learn the best practices and tools to ensure accurate measurements.
Precision and reliability are critical when it comes to monitoring pressure, especially in industries like water management, engineering, and safety operations. From preventing costly disasters to optimizing operational performance, accurate pressure monitoring ensures safety and minimizes risk. But how do you ensure your pressure monitoring systems are not only accurate but also safe?
This blog explores the principles of pressure monitoring, highlights the significance of technology in enhancing accuracy, and provides insights into choosing the right tools for the job.
Why Pressure Monitoring Matters
Monitoring pressure is essential in many sectors, from industrial processes to water management systems. Whether you’re managing pipelines, water distributions, or high-performance machinery, a failure in pressure management could lead to adverse effects, including equipment damage or safety hazards.
But the stakes don’t end there. Inefficient monitoring can cause production delays, inflated costs, or even environmental damage. By investing in advanced pressure monitoring technologies, safety managers and engineers can identify irregularities before they evolve into significant issues, ensuring operational fluidity and safety compliance.
The Fundamentals of Pressure Monitoring Systems
Understanding the inner workings of pressure monitoring systems can help you appreciate their precision. Most systems operate using sensors or gauges that measure the force exerted by liquids or gases. These measurements can offer insights for real-time decision-making, from maintaining water pressure in pipelines to controlling pressure in chemical processes.
However, for these systems to function flawlessly, accuracy is non-negotiable. Investing in tools ensures precise measurements by incorporating innovative technology. Unlike traditional analog gauges, digital pressure gauges provide clear readings, minimize human error, and are increasingly being adopted in technical landscapes.
The Role of Sensors in Accuracy
Sensors are the backbone of modern pressure monitoring technologies. They capture pressure variations and transform this input into actionable insights. Depending on the application, piezoelectric sensors or capacitive sensors are among the most trusted types used in industries.
Key advantages of reliable sensors include:
- Real-time alerts when pressure exceeds safe limits.
- Enhanced reliability in monitoring even in challenging environments.
- Reduced maintenance costs, thanks to improved fault detection algorithms.
Ensuring Safety Through Accurate Monitoring
Given the risks involved, particularly in industries dealing with flammable substances, safety becomes a prime concern. For water management professionals or engineers, understanding the pressure limits within your systems can reduce the likelihood of catastrophic failure.
Below are strategies to ensure both safety and precision in your pressure monitoring:
Regular System Testing
Test your systems periodically to identify calibration errors or faulty components.
Investing in Technology
Tools like digital pressure gauges provide advanced analytics and trend predictions, crucial for safety planning.
Set Alert Parameters
Identify threshold levels within your monitoring tools to trigger alarms or automatic shutdowns when necessary.
Perform Safety Drills
If pressure levels spike due to emergencies, simulated drills provide teams the preparedness required to act quickly.
The Technology Driving Modern Pressure Monitoring
The evolution of pressure monitoring tools has been game-changing for engineers and safety managers. From remote compatibility to intelligent algorithms, modern systems are equipped to not only record data but also analyze and interpret it.
Digital Transformation in Monitoring
With the introduction of IoT (Internet of Things) and AI, pressure monitoring technologies have become smarter and more accessible than before.
- IoT Integration allows remote access to real-time pressure data, ideal for large-scale operations like water plants or pharmaceutical industries.
- AI Algorithms predict potential deviations in pressure trends before they occur, mitigating risks in advance.
Additionally, having systems that interface seamlessly with cloud storage ensures that historical data can be easily accessed for future analysis. This digital transformation empowers decision-makers with the ability to prioritize preventive measures over reactive solutions—saving costs and time.
The Importance of Choosing the Right Monitoring Tools
Every application has its unique requirements; therefore, no single pressure monitoring solution fits universal needs. For instance:
- Water management systems often focus on corrosion-resistant tools to ensure longevity.
- Chemical manufacturing prioritizes functionality within extreme temperature ranges.
- High-pressure mechanical systems lean towards durability and precision.
Regardless of your application, always prioritize tools that align with industry standards and certifications. Checking reviews from reputable sources or consulting professionals can also help narrow down the choices.
Building a Culture of Safety
Beyond investing in advanced tools, fostering a safety-first culture is paramount. Safety is a collective responsibility among stakeholders, engineers, and team members. Encourage a workplace culture that values proactive audits, open communication regarding potential risks, and regular training sessions.
Additionally, integrating technology into your safety practices encourages employees to engage meaningfully. Real-time monitors linked to dashboards, for instance, demonstrate how their efforts can significantly improve operational safety standards.
Why Safety and Accuracy Are More Important Than Ever
Industries need to thrive in an era where risks are evolving faster than regulations. Ensuring accurate pressure monitoring isn’t just about preventing accidents but also about optimizing performance and maintaining credibility.
By leveraging tools like digital pressure gauges and implementing data-driven monitoring systems, businesses position themselves as industry leaders who prioritize both safety and operational brilliance.
If you’re a technology enthusiast, safety manager, or engineer eager to explore the latest tools and solutions, this is the ideal time to evaluate your pressure monitoring systems. Think smarter. Think safer.